Practicas de Incremento de Valor
Aseguramiento de Proyectos
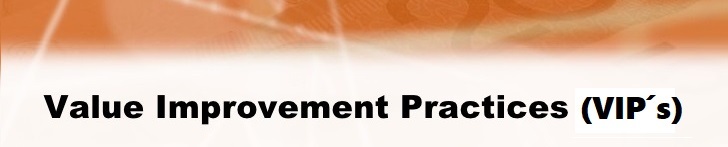
Los propósitos clave de la aplicación de las Practicas de Incremento de Valor durante el desarrollo de un proyecto de capital y el ciclo de vida de la implementación son: 1. Para mejorar el desempeño de los costos, 2. Para mejorar el desempeño del cronograma, 3. Para mejorar el potencial para el desempeño operacional efectivo, 4. Contribuir a mejorar el rendimiento del proyecto y 5. Alineación de expectativas entre las partes interesadas.
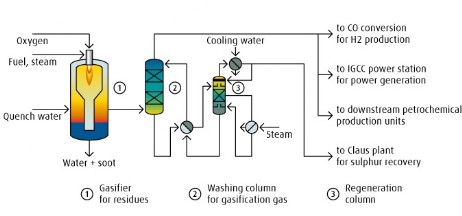
La selección de tecnología es un proceso sistemático para seleccionar las mejores opciones tecnológicas que cumplan con los objetivos del proyecto y mejoren nuestra ventaja competitiva.
El proceso de selección de tecnología es importante porque es una de las primeras actividades en el FEL de un proyecto. En esta etapa, las decisiones que se toman pueden tener un impacto importante en el éxito financiero del proyecto. La tecnología elegida sin un plan bien pensado puede llevar a sobrecostes, planificación más larga (especialmente al inicio) y oportunidades perdidas en el mercado.
Un enfoque del proceso es buscar fuentes externas de tecnología para romper el paradigma de "no se inventó aquí". Otra visión es convertirse en un "seguidor rápido" en la implementación de tecnología innovadora.
Un elemento clave en este proceso es utilizar un equipo multifuncional para garantizar que se cumplan las expectativas de negocios, técnicas y de fabricación. La mezcla de personas también facilita la generación de una lista más amplia de tecnologías para evaluar. El proceso se puede aplicar para seleccionar la tecnología general del sistema, por ejemplo, la Unidad FCC o para equipos discretos, por ejemplo, un compresor.
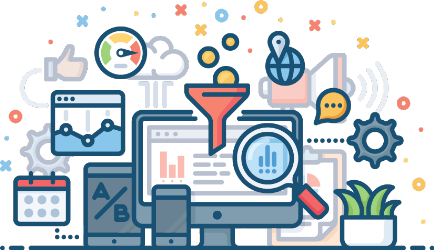
Simplificación de Procesos es un taller estructurado que se enfoca en simplificar la fase de desarrollo, las instalaciones, el procesamiento o los requerimientos del equipo mientras se satisface la funcionalidad necesaria para brindar resultados comerciales.
La simplificación del proceso se puede aplicar a instalaciones nuevas o existentes para mejorar el capital, los costos de operación y mantenimiento, la calidad del producto final, la capacidad y flexibilidad de producción, la reducción de desperdicios, la respuesta del cliente y la reducción de inventario. La simplificación de procesos se centra en eliminar pasos innecesarios y optimizar el número de trenes y asignaciones de redundancia, junto con la flexibilidad operativa. La simplificación del proceso a menudo se lleva a cabo junto con el Diseño por Capacidad
Clases de Calidad de la Planta es una práctica para establecer qué calidad de instalación se necesita para cumplir con los objetivos comerciales. Ajusta la confiabilidad, la capacidad de expansión, la automatización, la vida útil de la instalación, el factor de flujo esperado (SF = No. de días que la planta opera por año/365), la probabilidad de expansión, cambio de la tasa de producción en el tiempo, la calidad del producto y la flexibilidad del producto. La clase de calidad de la planta se puede utilizar para determinar las asignaciones de diseño necesarias, la redundancia, la filosofía de ahorro y el espacio para la expansión.
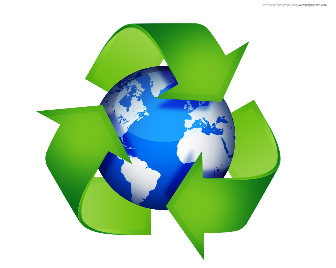
Minimización de Residuos es un proceso por el que se realiza un análisis para desarrollar conceptos y propuestas para reducir o, mejor aún, eliminar cada flujo no útil. Este análisis se realiza antes de que el alcance del proyecto sea firme.
En los últimos años, las empresas de la industria de procesos químicos han cambiado sus esfuerzos ambientales de controlar las descargas después de que se generaron para prevenir la generación de emisiones y desechos en primer lugar. El énfasis ha pasado del tratamiento al final de la tubería a la reducción de desechos en la fuente y/o la reutilización de desechos como métodos de manejo de desechos más rentables. La jerarquía de eliminar o reducir el desperdicio se puede describir como sigue:
Prevención:
Análisis de minimización de residuos completado?
Reciclar/Reutilizar:
Se pueden reciclar los flujos de proceso?
Reducción:
Se han evaluado las opciones del proceso de reducción de residuos?
Tratamiento:
Tratamiento mínimo de residuos esenciales e identificación de métodos de eliminación?
Este enfoque se ha utilizado con éxito en muchas instalaciones existentes. Desafortunadamente, no siempre es posible minimizar el desperdicio en la fuente o reutilizarlo en una instalación existente en la medida en que sea deseable. Si la estructura física de una instalación existente ya está establecida, esto limita de manera inherente la flexibilidad y las opciones disponibles para reducir o reutilizar los desechos.
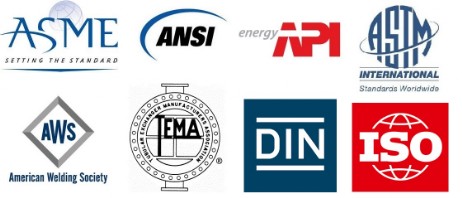
A veces, el costo de una instalación se incrementa mediante la aplicación de códigos, normas y especificaciones que exceden las necesidades reales de la instalación específica que se está diseñando.
En los primeros días evolutivos de la industria química, la uniformidad de los estándares de diseño no estaban bien definidos. Como resultado, muchas compañías líderes desarrollaron sus propios estándares basados en su experiencia y conocimiento interno. Con el paso de los años, estos estándares se hicieron rígidos e inflexibles. En tiempos más recientes, los estándares de diseño se han modernizado y aceptado ampliamente en toda la industria.
Existen varias consideraciones para decidir qué estándares y especificaciones usar en un proyecto. Por ejemplo, los estándares internos de una compañía con respecto a los materiales de construcción únicos para un diseño específico pueden ser mejores que un estándar genérico, más general. Sin embargo, a veces el costo de una instalación se incrementa mediante la aplicación de códigos, normas y especificaciones que exceden las necesidades reales de la instalación que se está diseñando. Los costes también pueden ser inflados por la insistencia en estándares únicos de la compañía cuando existen estándares aceptables de la industria.
Otra consideración es la adquisición de equipos. Un diseño de proceso único durante el desarrollo temprano de una tecnología a menudo requería equipos que fueron construidos de acuerdo con una especificación de diseño específica. Sin embargo, no hay duda de que la adquisición de equipos que cumplan con una especificación de diseño específica es mucho más costosa y consume más tiempo que la compra de equipos estandarizadoslistos. Esta Practica de Incremento de Valor debe incluir una consideración estructurada de las necesidades del proyecto y la selección de los estándares y especificaciones que satisfagan de manera óptima esas necesidades.
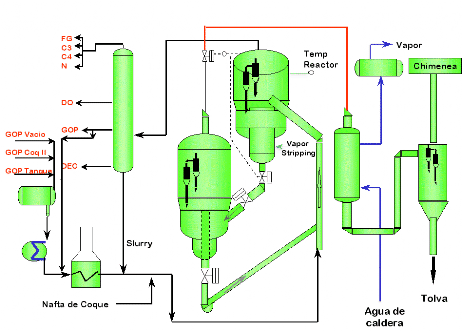
Diseño por Capacidad evalúa la verdadera capacidad máxima requerida de cada equipo importante en relación con la capacidad total deseada de la instalación. A menudo, el equipo está diseñado con un "factor de diseño" que da como resultado un equipo más grande y cierta capacidad adicional. Este conservadurismo puede llevar a que ciertos equipos o plantas enteras tengan un exceso de capacidad que la empresa puede querer o no pagar inicialmente.
El exceso de capacidad de procesamiento se incorpora a los diseños de varias maneras. El problema clave de no usar un buen enfoque de diseño a capacidad es que el exceso de capacidad incorporado en un diseño inadvertidamente es siempre ineficiente. Como resultado, mucho tiempo después se dedica a desestimar un diseño que debería haber sido creado para la expansión o ha sido imposible de desenclavar. El diseño por capacidad, como se define aquí, se centra en:
- Incertidumbre en la futura materia prima.
- Propiedades físicas
- Especificaciones del producto
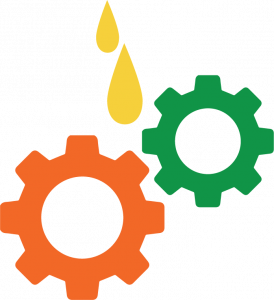
El Modelado de Confiabilidad de Procesos es una técnica de simulación para examinar los objetivos de operatividad de una instalación. Normalmente, se necesita un software especializado y/o un consultor.
El modelado de confiabilidad de procesos se basa en métodos tradicionales de ingeniería de confiabilidad.
Si las fallas ocurren o no y su tiempo hasta que ocurren, rara vez se puede pronosticar con precisión. Por tanto, la fiabilidad es un aspecto de la incertidumbre de la ingeniería. Si un elemento funcionará durante un período en particular es una pregunta que puede responderse como una probabilidad. Esto da como resultado la definición de confiabilidad de ingeniería habitual como:
La probabilidad de que un equipo realice una función requerida sin fallar en las condiciones establecidas durante un período de tiempo establecido.
La confiabilidad también se puede expresar como el número de fallas durante un período.
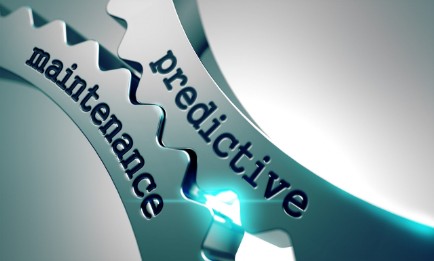
El Mantenimiento Predictivo es un enfoque para el mantenimiento de una instalación mediante el cual se monitorea el equipo y se realizan reparaciones antes de fallar. Por lo general, un enfoque de este tipo requiere agregar varios dispositivos de medición para evaluar las características operativas.
Tradicionalmente, los ingenieros de mantenimiento han combinado muchas técnicas, tanto cuantitativas como cualitativas, en un esfuerzo por predecir fallas inminentes y mitigar el tiempo de inactividad en sus instalaciones de fabricación. El mantenimiento predictivo les ofrece la posibilidad de optimizar las tareas de mantenimiento en tiempo real, maximizando la vida útil de sus equipos sin interrumpir las operaciones.
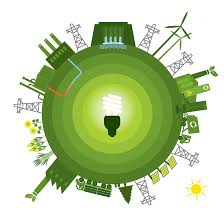
La optimización de energía (OE) es una metodología para optimizar el costo de capital, el costo operativo y la operabilidad de una unidad de proceso, sistema de servicios públicos o sitio de fabricación. Utilizando los datos termodinámicos básicos para los procesos, se pueden determinar los objetivos de consumo de energía y generación de energía que tienen en cuenta el costo del equipo.
El propósito de un estudio de OE es mejorar el retorno de la inversión para proyectos mediante la identificación de los niveles más económicos de recuperación de calor y generación de energía.
Varios clientes de IPA han utilizado con éxito el OE para el descongestionamiento de unidades de proceso (modernizaciones o renovaciones) restringidas por la capacidad de la caldera o del calentador de proceso, así como para optimizar los diseños de proceso para unidades nuevas. La metodología también se puede utilizar para optimizar el uso de energía en todo el sitio o para corregir desequilibrios de energía en sitios existentes.
Aunque una OE generalmente se asocia con la conservación de energía, también puede llevar a costos de capital reducidos, especialmente en unidades de proceso nuevas. Esto se debe a que la metodología se puede utilizar para identificar los arreglos de equipos más simples de una gama de opciones que tienen un rendimiento operativo similar.
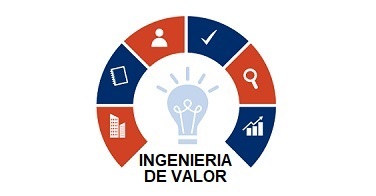
La ingeniería del valor es un método sistemático para mejorar el "valor" de los bienes o productos y servicios mediante el uso de un examen de función. El valor, tal como se define, es la relación entre función y costo. Por lo tanto, el valor puede ser manipulado mejorando la función o reduciendo el costo. Es un principio primario de la ingeniería de valores que las funciones básicas se conserven y no se reduzcan como consecuencia de buscar mejoras de valor.
Para Ingeniería de Valor, unas técnicas que parece apropiadas para cualquier tipo de proyecto ya que permitirán dar importancia a las características y características subjetivas de los sistemas alternativos que no son abordables en términos de costo puro son las técnicas de ponderación de criterios y matriz de análisis de alternativas.
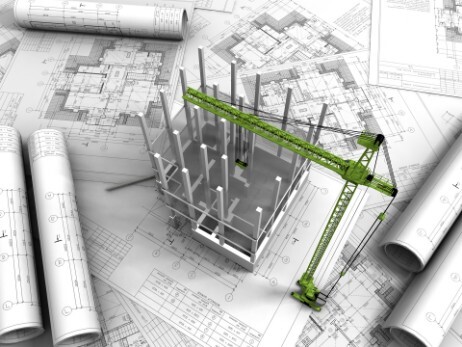
Análisis del diseño generalmente realizado por profesionales de construcción experimentados con la intención de reducir costos o ahorrar tiempo en la fase de construcción
Por lo general, las revisiones de constructibilidad involucran a profesionales de la construcción competentes que revisan los planos y diseños después de que el diseño está esencialmente completado y donde los cambios resultantes son modificaciones menores para garantizar la viabilidad de la construcción. Incluso en lugar de un programa más amplio, tales revisiones pueden proporcionar beneficios significativos. Sin embargo, se obtienen beneficios mucho mayores cuando un programa de construcción involucra a los profesionales de la construcción de manera más o menos continua, comenzando en la etapa conceptual del proyecto y continuando hasta la finalización del diseño. En un programa de este tipo, la gente de la construcción funciona como parte del equipo de diseño del proyecto. Como tales, están involucrados en el esfuerzo total de diseño, en lugar de limitarse a si un diseño completo puede construirse fácilmente o no. Ellos trabajan con los ingenieros para planificar la mejor manera de alcanzar el resultado final deseado.
Un proyecto que utiliza un programa de constructibilidad cambia el enfoque de la planificación y programación de ingeniería. Los trabajos de ingeniería y construcción se planifican juntos, y las necesidades de construcción a menudo conducen el enfoque de ingeniería. Esto puede implicar apartarse de la secuencia de diseño normal para que los entregables de ingeniería atiendan mejor las necesidades de construcción. Es posible que se necesiten diseños inusuales para permitir que la construcción funcione en un espacio limitado.
Los detalles de ingeniería están diseñados con el aporte de construcción inmediato para optimizar más estrechamente los costes del proyecto. En cualquier caso, el resultado es un plan general del proyecto impulsado por las necesidades comerciales del propio proyecto. Los cronogramas de ingeniería se elaboran en base a una visión holística de las necesidades del proyecto, incluidas las secuencias de construcción óptimas, en lugar de que los cronogramas de construcción se basen en el tema de dibujo prometido y las fechas de entrega de material.
El inicio de un programa de constructibilidad en el momento adecuado proporciona una secuencia de construcción temprana, la determinación de la secuencia de un problema de dibujo, la determinación del trabajo de detalle mínimo necesario para impartir adecuadamente las necesidades de diseño a la fuerza de construcción, etc. La constructibilidad garantizaría los diseños del sitio que brindan acceso a la grúa, espacio de disposición adecuado y áreas de preparación, acceso para materiales y personal, y evitar limitaciones innecesarias en los métodos de construcción. Los diseños detallados serían orientados para evitar dificultades en la construcción.
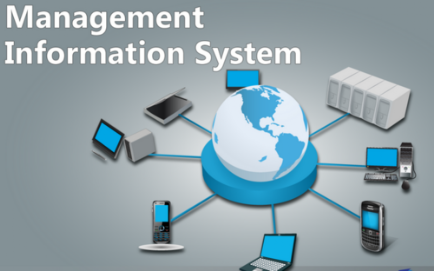
Ciclo de Vida de la Ingeniería - Gestión de Información (CAD 3D) es el proceso de gestionar toda la información de ingeniería, a través del ciclo de vida de la misma.
Originalmente, los datos de ingeniería eran relativamente simples: archivos de diseño, listas de piezas y especificaciones. En ese momento, el software de gestión de datos de ingeniería [Engineering Data Management Software (EDMS)] y, posteriormente, la gestión de datos de productos [Product Data Management (PDM)] permitían a los usuarios organizar sus datos de productos y aplicar reglas para la identificación de artículos y el control de revisiones. Una biblioteca de datos electrónicos asociada contenía archivos CAD 2D/3D y otros archivos de diseño.